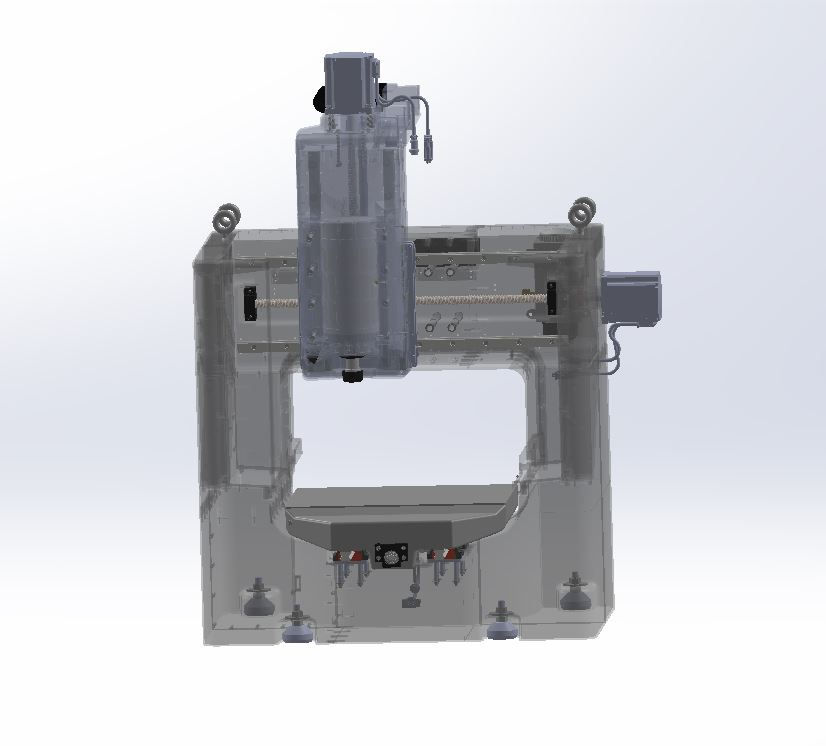
CAD model of the full machine
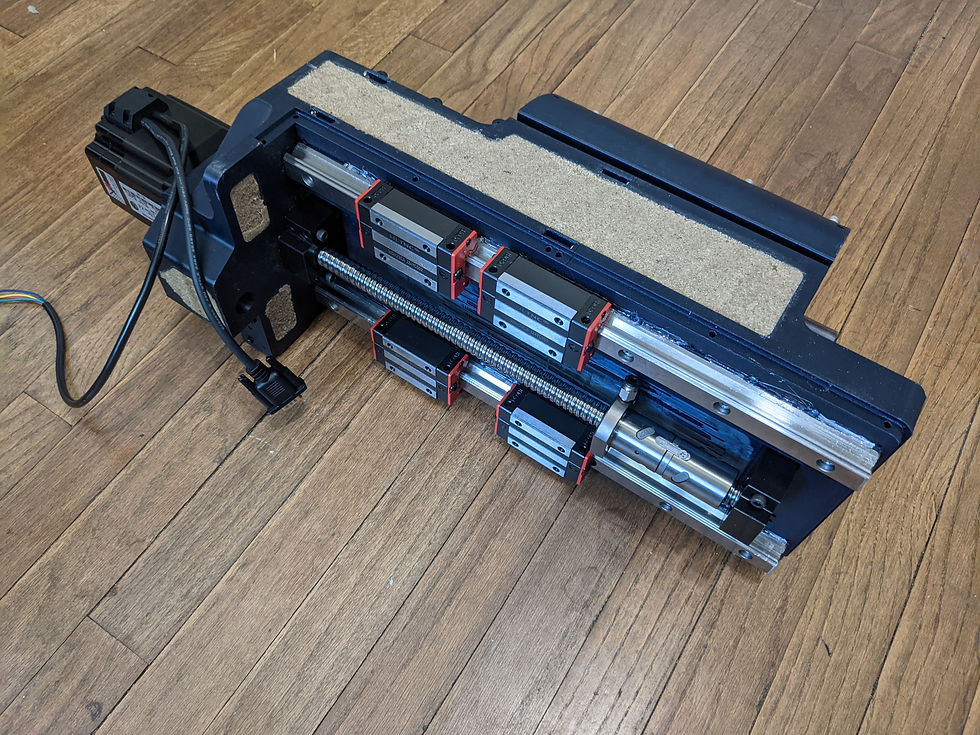
Headstock cast and partially assembled

Welded steel table (primed but not finished) for holding the machine and housing electronics/coolant
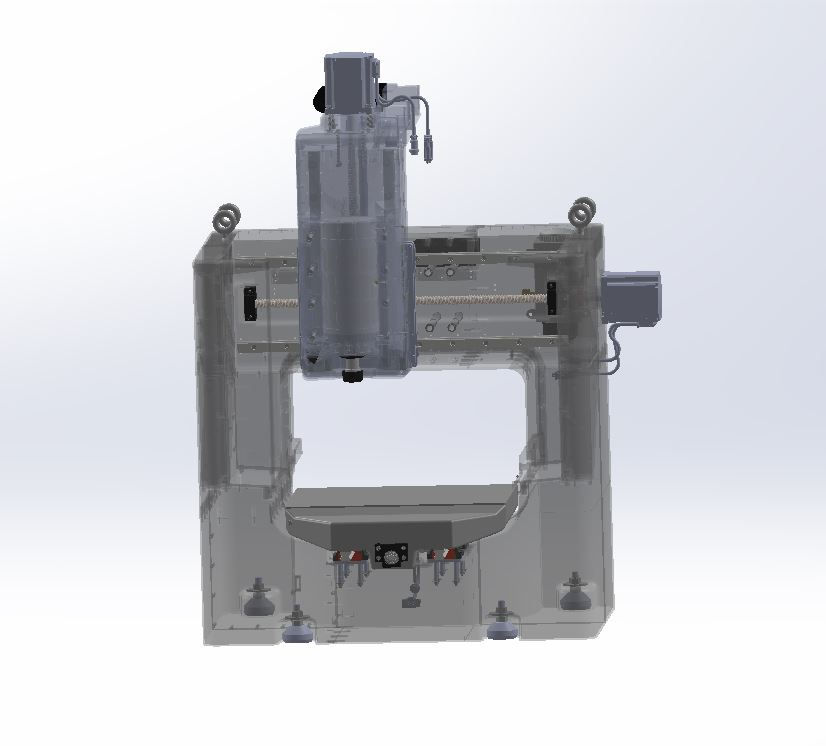
CAD model of the full machine
Desktop Milling Machine
For the past year, I’ve been working on building a desktop CNC machine. The machine’s structural components are made by casting an epoxy-silica composite into permanent 3D-printed shells. To hold the precision hardware accurately during casting, I use inexpensive but precise fixtures. My goal is to develop this method into a cost-effective, accurate approach for creating DIY CNC components without requiring precision machining.
​
So far, I’ve cast the bed and headstock components with promising results. That said, this project has been highly challenging (and ongoing), and there are still several areas where I need to refine both the process and design.
To design the frame of this machine, I utilized various simulation techniques, including finite element analysis (FEA) and topology optimization. The manufacturing process I’m employing provided greater flexibility to optimize the shape of the machine components. To the right you can see some of my simulations and how they informed my frame prototype models as I progressed through the design.


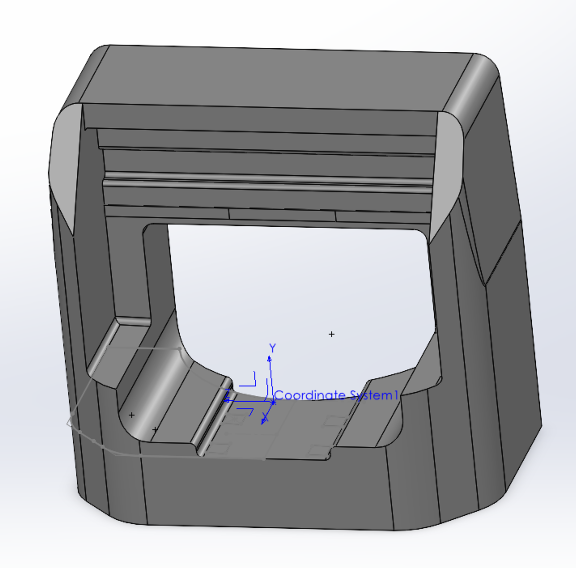
